Table Of Content
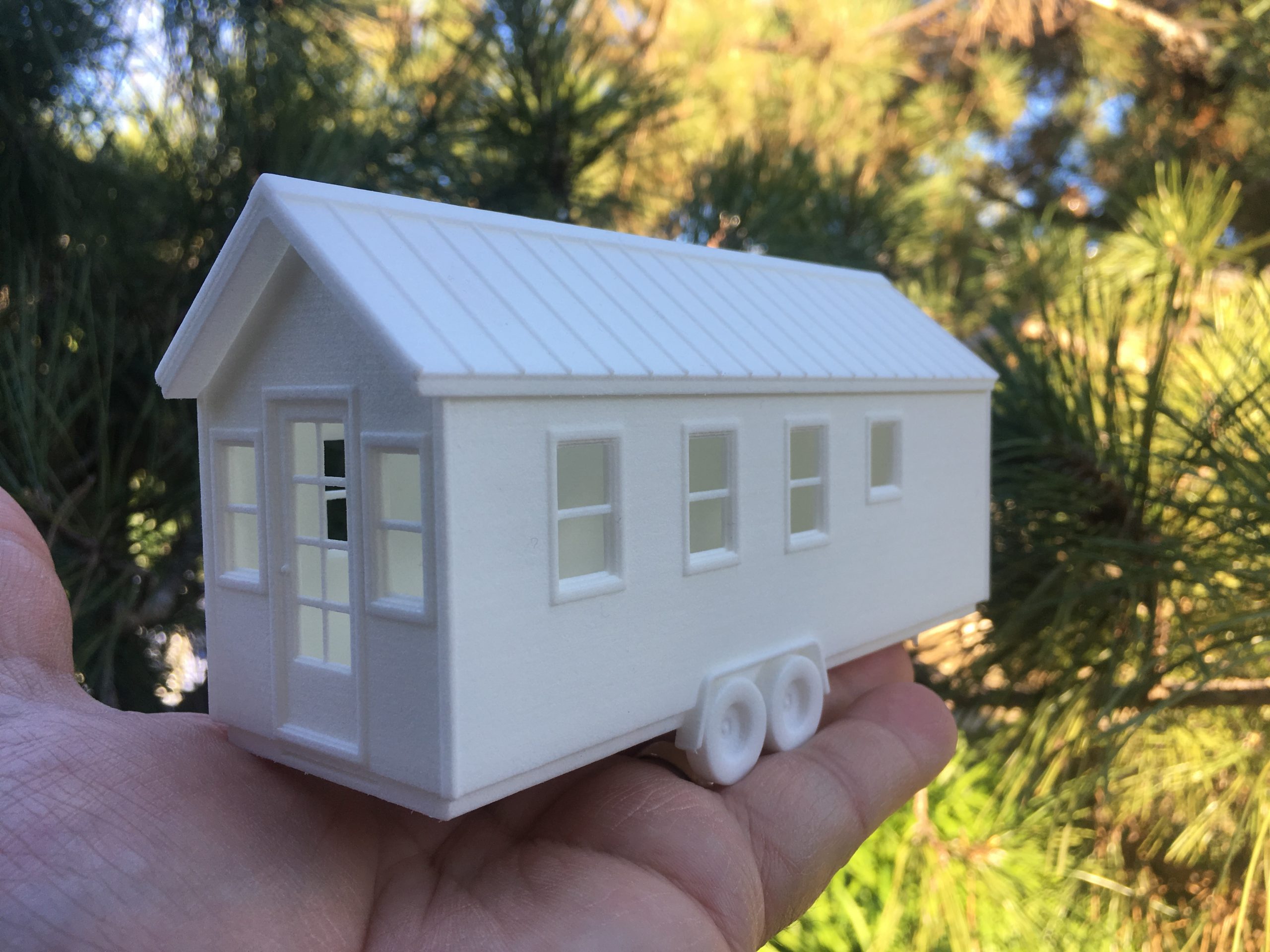
It's obviously relatively basic compared to other 3D-printed houses we've seen, like the more high-end Wolf Ranch models, though it's also around $400,000 cheaper, so is focused toward a totally different market. Located in the Greater Porto area of Portugal's second-largest city, the unnamed 80 sq m (roughly 860 sq ft) two-bedroom residence was built using COBOD's BOD2 printer, which was also used on Europe's largest 3D-printed building. According to COBOD, Havelar's houses can be produced for €1,500 per sq m, which it contrasts favorably with the Porto average of €3,104 (around US$3,330) per square meter.
What It’s Really Like to Live in a 3D-Printed Home
New Story is Co-Founded and advised by some very powerful and successful people, including Glassdoor’s CEO, and Reddit Co-Founder Alexis Ohanian. Many of the people attached to the project have a track record of execution and success, so we look forward to seeing the project’s progress. Since the Texas project they have also printed a series of 3D printed houses in Mexico. Another recent viral story, this collaboration between ICON and New Story made headlines when they 3D printed a house in Texas, USA earlier this year. The prototype 3D printed house built cost the companies approximately $10,000, though they assert that this number can be brought down to $4,000 going forwards. Probably the most famous and viral 3D printed house build, this interestingly shaped house was built back in 2017 in just one day – while it snowed!
House 3D Printer Companies To Watch in 2024
In addition to manufacturing and selling the equipment, the company also offers “printing-as-a-service” (PaaS) for an additional revenue stream. In other states, like Texas, Colorado and Virginia, 3D printed homes have already made their way to market. Just north of Austin, there’s a whole neighborhood of 100 3D printed homes underway. But there are questions around installing reinforcements and weather-resistance that many researchers are still in the process of answering. Since then, they’ve built a sleek 24m2 house in Valencia, as well as a 32m2 house they 3D printed in 12 hours for the Morroco-based Solar Decathlon Africa event in 2019 – winning the prize for most innovative start-up. Help us tackle housing and climate crises by building sustainable, beautiful, and mighty homes.
printed houses, commercial buildings, infrastructure, and more
Over in Wallenhausen, Germany, German-based construction company PERI Group started construction on a 3D printed three-story multi-family apartment building, following the success of the two-story home they printed earlier that year. This is in conjunction with their new East 17th Street initiative, a project that hopes to use this innovative technology to build a small community of 3D printed homes in the growing area of East Austin. The University of Maine just revealed the world’s largest 3D printer, and it is an absolute beast.
A document published by COBOD, a Danish company that is a global leader in 3D printing solutions for the construction industry, warns consumers by taking stock of what 3D construction is really like today. For example, it mentions the company Winsun, which claims to have built 10 3D buildings in 10 days. In fact, they assembled 10 buildings in 10 days, from 3D printed components produced in a factory long before. For many media outlets, one reason for 3D printed houses is to help people struggling to find housing, since they are supposedly cheaper and faster to build (which is not necessarily the case, as we just saw). That said, "the housing problem has never been technological, it's social and economic, whether you're in San Francisco or the Salvator," says Lloyd Alter. As tenants move into 3D-printed houses in the first years of their commercial listing debut, 3D printing is on a 23 percent compound annual growth rate over the decade to come, according to Grand View Research.
Standardized Sustainable Homes, Enhancing Canada's Housing Landscape
A reality synonymous with smart manufacturing, 3D printing makes up a prominent part of Industry 4.0 remolding construction as we know it. While ICON is pursuing some “off-world construction” projects, it hasn’t slowed down on its earthly endeavors. In fact, the research from the NASA projects is helping the team develop better, more eco-friendly building materials. Proponents of the technology say 3D printing could address a range of construction challenges, including labor shortages and building more resilient homes in the face of natural disasters. Personally, I like the living room designs that are open concept and include a kitchen nook within the living room space.
Beautiful homes, healthy planet
Cleverly placed doorways and windows bring in more sunlight, giving the interior and aesthetic appeal while reducing the need for artificial daytime lighting. Village, ICON launched the Genesis Collection, a housing project of 100 3D-printed family homes. And the best part is that the project will source all raw materials directly from the moon’s surface and print them using a revolutionary 3D printer that ICON is developing. ICON have also pioneered research into their concrete-based material to prevent it creating imperfect layers or hardening too quickly. The actual material mix itself can be altered based on needs and uses, making ICON’s offering versatile and changeable based on the local environment.
3D Printed Houses: 9 Top Examples - Built In
3D Printed Houses: 9 Top Examples.
Posted: Mon, 01 Apr 2024 18:20:12 GMT [source]
The World's Largest 3D Printer Unveiled In The US, Can Print A house In Under 80hrs - Indiatimes.com
The World's Largest 3D Printer Unveiled In The US, Can Print A house In Under 80hrs.
Posted: Sun, 28 Apr 2024 05:00:12 GMT [source]
Alquist is the only 3DCP company that has the knowledge to work directly with local city officials, passcode and permitting, and successfully print a home using multiple printers and/or materials. Italian house 3D printing company WASP built ‘Gaia’, a 3D printed hut made from a mix of concrete and mud-based material. The 215 square foot structure took 10 days to complete, though the total time when accounting for all the furnishings and additions would be longer. The most extraordinary part is that the hut cost just $1,000 in materials to build, though this doesn’t factor in labor and other costs. Designing the exterior of your 3D printed tiny house comes with lots of creative freedom.
BC Gov Announces Next 20 Cities To Receive Housing Targets
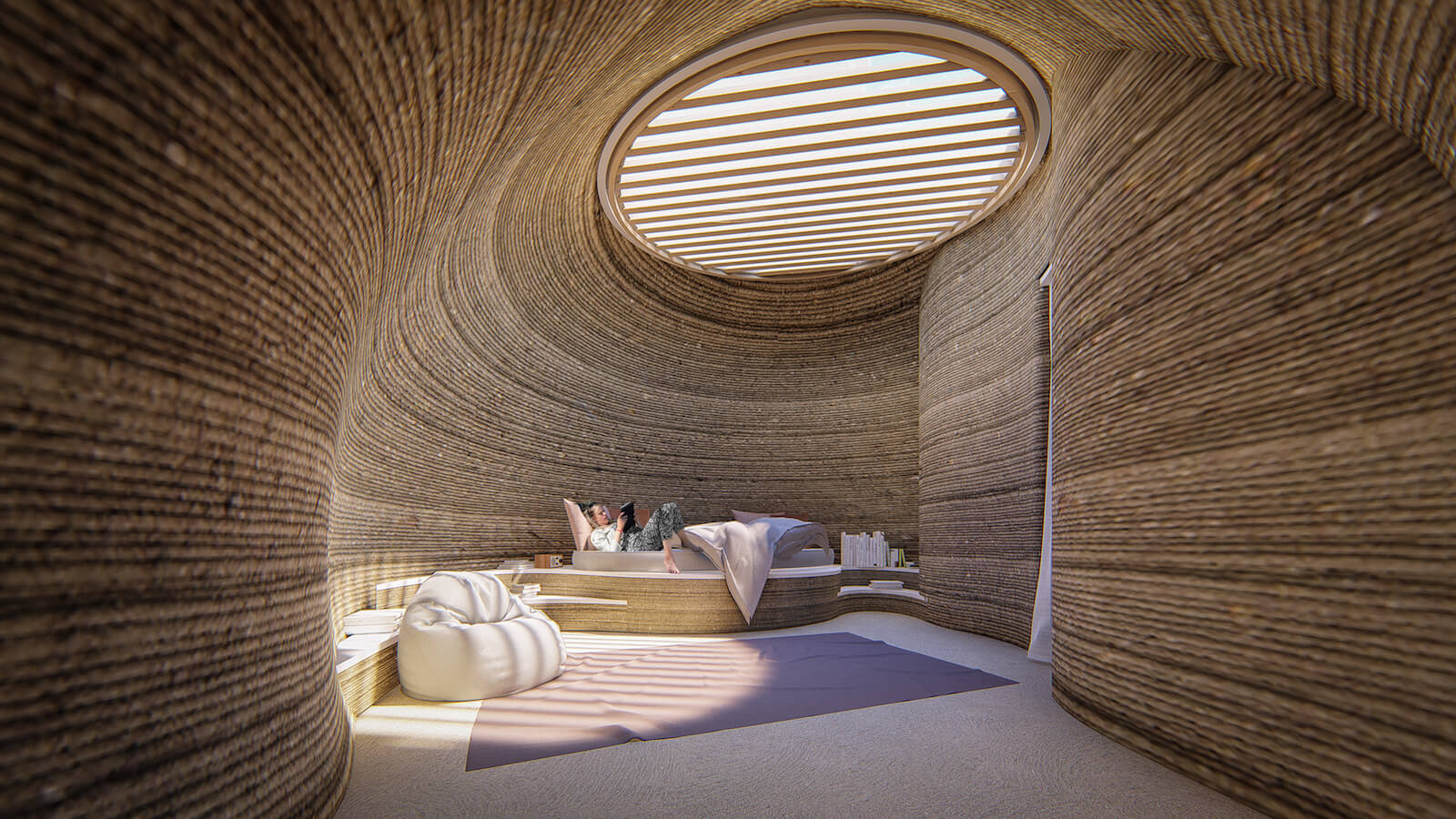
Dubai have been championing ambitious architectural projects for years, and have recently made the bold move of aiming to have 25% of new buildings 3D printed by 2030. We also discuss the key advantages of 3D printing houses versus traditional housebuilding later on in the article. The two printers can be used in concert to streamline manufacturing by working on the same project — or even part if necessary — and there will be even more of them working together in the future, officials said. Such printed buildings can be recycled, which is unique compared to current construction. "You can basically deconstruct it, you can grind it up if you wish, the 3D printed parts, and reprint with them, do it again," Dagher said before the event. While it’s hard to deny the possibilities of 3D-printed military vehicles, I’m far more excited about the possibilities that become available for housing the homeless and creating more sustainable housing for people all over the country.
While the idea of 3D printing housing may have seemed far-fetched not that long ago, they are quickly becoming easier to build in our increasingly tech-dependent world. Building a 3D printed tiny house can be more cost effective, time efficient, and just as structurally durable as a traditional home. In development with 3D-printing firm WASP, Italy-based studio Mario Cucinella Architects set out to create bioclimatic, low-carbon proof-of-concept housing in response to escalating climate emergencies and housing crises worldwide. Standing out from the crowd, Tecla’s tan, double-dome structure is constructed out of 350 layers of locally sourced clay from a nearby riverbed. A portmanteau of “technology” and “clay,” Tecla is a 538-square-foot structure that stands at about 15 feet tall and features two skylights.
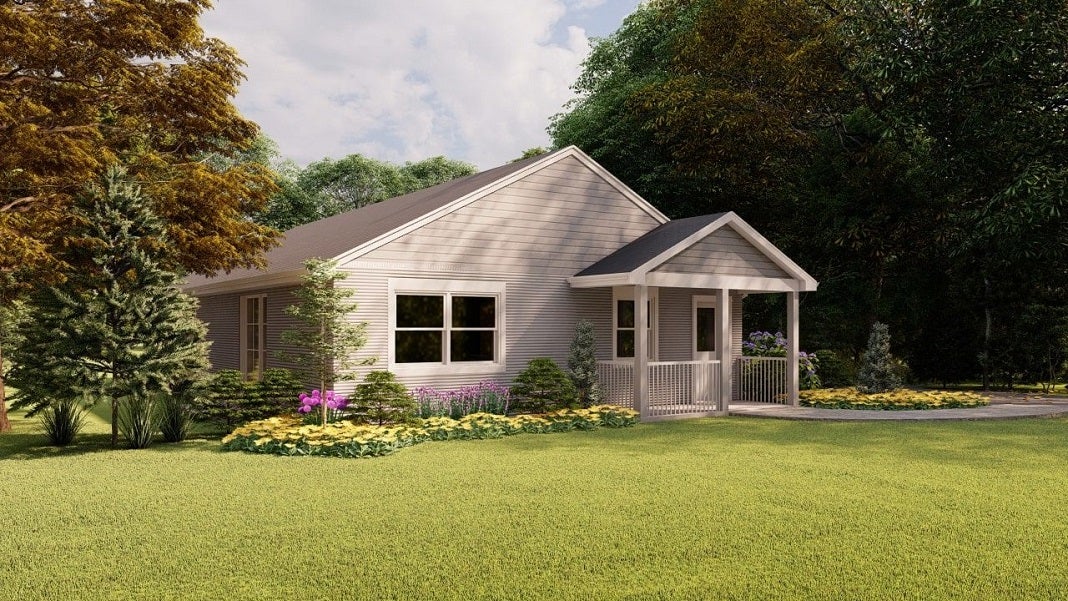
As with any building project, the first step to building a 3D house is to grade and level the land. Investing in a north-facing plot with high-quality soil will be your best bet for a strong and sturdy build. ARCS’ 3D-printed-concrete compressive strength tests exceed the industry standard by double.
Our kit system design quickly delivers almost any floor plan, and our 3D printing capabilities offer unique exterior design possibilities. 3D printing and our composite stone material - made from 60% recycled glass - allow us to build walls with less material and eliminate 99% of waste. These materials are eco-friendly and can be easily melted and extruded by the printers. Additionally, composite materials, such as a combination of fibers and resins, are being explored for their high strength-to-weight ratio and flexibility in design. Weaving together ancient building techniques with modern technology to form recyclable, low-carbon, climate-adaptable housing – “we like to think that Tecla is the beginning of a new story!
Benoit Furet, the man behind the project, believes 3D printed houses offer a solution to the growing housing shortage and for social housing in the future. Moreover, he claims that with growing economies of scale and technological advances, 3D printed houses will become 40% cheaper to build in years. The first 3D-printed affordable housing project in Canada, which is tentatively called “Sakura Place,” will see a cluster of five three-bedroom homes which come together to form the petals of a cherry blossom. The plan was to start in the summer, but Comishin says their building permit has been delayed. Their latest model, the CyBe G, is gantry-based with a four-column, three-beam configuration, ideal for affordable housing construction.
Bologna-based architecture studio Mario Cucinella Architects and 3D-printing specialists WASP collaborated to create a 60-square meter low-carbon housing prototype named Tecla – a combination of the words technology and clay. The entire building, including its roofs and foundations, is made of low-cost real concrete using a large construction 3D printer by COBOD. Its curved, sloped exterior walls have been constructed through printing layers of stacked concrete to form 24 individual components.
No comments:
Post a Comment